UV打印成品出现表面发粘、附着力差等问题,往往源于固化系统异常。这种现象在深色材料打印、厚墨层作业时尤为明显,直接影响产品耐候性和商业价值。以下为典型故障排查指南:
1. 能量密度不达标:UV灯每使用800小时光强衰减15%,建议使用UV能量计定期检测(标准值:透明墨水≥350mJ/cm²,白色墨水≥550mJ/cm²)。老化灯管及时更换,汞灯与LED固化系统需区分检测标准。
2. 反射罩氧化失效:铝制反射罩使用6个月后反射率下降40%,表现为灯管发热量异常升高。可用镜面检测卡观察光斑均匀度,出现条纹状阴影需立即更换。建议选用镀金陶瓷反射器,寿命延长3倍。
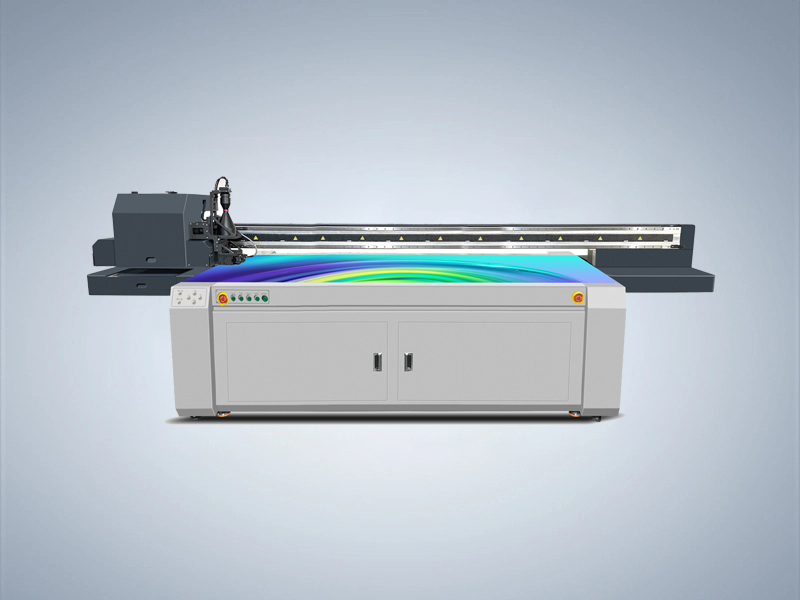
3. 打印-固化间距失准:介质表面与UV灯最佳距离为8-12cm。打印浮雕效果时,需同步调整固化系统升降机构,距离误差超过±2cm会导致30%以上能量损耗。
4. 墨水透光率不匹配:打印黑色亚克力等吸光材料时,需选择含光引发剂的深色专用墨水。第三方墨水建议做透光率测试,380-420nm波长透光率应>15%。
5. 冷却系统异常:汞灯工作时温度需稳定在700±50℃,采用双循环水冷系统时,定期检测冷却液电导率(标准值<5μS/cm)。管路积垢达0.5mm厚度时,散热效率下降60%。
6. 介质预处理缺失:PET、PP等非极性材料打印前必须进行等离子处理,达因值需提升至42mN/m以上。现场可用达因笔快速检测,未达标材料需返工处理。
建议每季度使用分光光度计检测固化度,重点监控白色墨层的Tg值(玻璃化转变温度)。当出现局部固化不良时,可尝试降低打印速度20%并开启二次固化模式。通过建立能量-温度-间距三维参数模型,可使UV固化效率提升至98%以上。